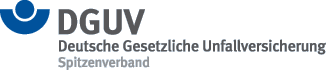
completed 06/2020
ISO TS 15066 states biomechanical load limits for the evaluation of collaborative robots featuring protection in the form of power and force limiting (EN ISO 10218). Evaluation of workstations employing collaborative robots requires measurement with a biofidelic force/pressure measuring instruments. This instrument must be capable of measuring both the force over time and the pressure distribution, and at the same time of simulating the mechanical resilience of the human body. The standard also states typical deformations/rigidity for different body regions. It does not however contain precise provisions concerning the measurement arrangement and possible measurement uncertainties. This may result in existing force/pressure measuring instruments returning different measurement results for the same load. This could in turn lead to distortion of competition, and be detrimental to the objective of protection. It must be ensured that the measuring procedure followed is the same when different force/pressure measuring instruments are used, irrespective of the manufacturer, and that comparable measurements are obtained at a given load. This project therefore identified the principal measurement and instrument parameters and developed detailed provisions for a harmonized instrument specification. The activities supported the development of a measurement protocol, recognized throughout the EU, for verification of force and power-limited robots. The COVR toolkit (www.safearoundrobots.com) was employed for this purpose.
An existing test arrangement developed at the IFA was returned to use. The test arrangement enabled force/pressure measuring instruments from a number of manufacturers to be loaded mechanically by means of an electromagnetically driven actuator fitted with a plunger/tappet. Selective manipulation of a force/pressure measuring instruments enabled a range of effects to be demonstrated and the effect of various parameters determined. At the outset, possible parameters were identified in a literature study. A plausibility test was simulated with an initial version of a simplified spring/damper/mass system in MATLAB-Simulink. Experiments employing a mechanical pendulum were also conducted. These permitted comparison between different instruments. Three types of instruments in a number of variants (combinations of compression elements) have been compared to date. Further types and variants can be included in the comparison in future.
The influence of the different compression elements fitted to the measuring instruments upon the measurement results obtained was demonstrated. Deviations of generally between 5 % and 10 % were observed for different measuring instruments under identical loads. These deviations, which are caused by the mechanical properties, are greater than the (electrical) measurement uncertainties stated by the manufacturers. Rigidity characteristics of the different variants of the instruments were also recorded. Correct measurement requires the characteristics of the biofidelic force/pressure measuring instruments to resemble the mechanical compliance of the human body as closely as possible. We recommend that this be checked, since there is evidence of further scope for improving this correspondence for some variants. It was also shown that the moving mass of the measuring instruments, a function of their design, has a significant influence upon the vibration behaviour. This parameter has not yet been considered in the literature. The resilience of the measuring instruments mount also influences the measurement signal characteristic; measuring instruments should be mounted as rigidly as possible in the interests of comparable measured values being attained. An EU-wide project is to incorporate the findings into the guidelines for robot safety. The results have been used to modify a measurement protocol in the COVR toolkit (www.safearoundrobots.com). The protocol helps users to check and document the validity of their robot application properly.
-cross sectoral-
Type of hazard:mechanical hazards
Catchwords:accident prevention, test method, mechanical hazards
Description, key words:human-robot collision, collaborative robots, force/pressure measuring instruments, power and force limitation, measuring methods, force measurement, EN ISO 10218, ISO TS 15066, mechanical hazards