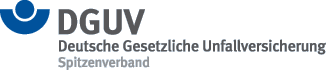
completed 12/2000
Safe tools are conditio sine qua non for the increasing use of high-speed processing as innovative procedure. Tool safety problems result from the process dynamism which is increased by a factor of 5-10 (e.g. milling speed, revolutions, and advance). In contrast to conventional milling, fast rotating tools are subject to substantially higher centrifugal forces which, as a rule, may exceed the processing forces by up to a power of ten. Therefore, a failure caused by centrifugal force represents a strong hazard for operating personnel and environment. Up to now, there are hardly any findings about operational strength of such tools in the event of cyclic load; here, apart from static strength, also material fatigue gains significance. It is particularly the tool basic body which, when bursting, releases high damaging energy amounts, so that the basic body is required to remain operationally stable during its period of use, i.e. that there shall be no failure relevant material fatigue. The increased use of aluminium alloys as basic body material gives this issue particular importance.
It was the objective of the campaign to use studies on cyclic load as a basis for developing easily usable calculation and estimation methods for operationally stable or permanently stable dimensioning tool bodies made of aluminium alloys. Furthermore, this campaign was intended to serve for further development of tool safety standardization. Additionally, the campaign offered the possibility to place the systematically compiled knowledge and the existing test stand units as well as the calculation systems at the disposal of small and mediumsized enterprises.
The campaign was divided up into three essential sections and contained theoretical, constructive and experimental work. The theoretical section of the campaign made an analysis of the weak points of tool basic bodies as laid down in DIN 8030, expressed model regularies for the design of test rotors, defined the trial matrix, made a theoretical determination of parameter functions of the component's capability to withstand stresses and loading, defined a damage accumulation approach, adapted the theoretical characteristic of the component's capability to withstand stresses and loading to the experimentally found characteristic function (Wöhler lines of the component), and adapted the damage accumulation approach for modified load cases using results of the experiments. Within the framework of constructive works, trial rotors were designed and constructed. The experimental works included determination of component's Wöhler lines in the single stage centrifugal force load experiment with increasing load, and determination of the lifetime lines for defined multistage load cases with tension ratios.
Within the framework of the campaign the torque stability of tool bodies made of the aluminium alloy AIZnMgCu 1,5 was examined depending on the number of the centrifugal force load cycles run through. The experimental studies were performed on various samples and examination methods analysed on the basis of the real tool load with the help of consideration of similar mechanisms.
During the campaign, it was possible to examine and work up the issue within the framework of inter-universitarian cooperation. The tool manufacturers will directly benefit from those results which are worked up and implemented characteristics, calculation approaches and design in form of recommendations. Regular campaign meetings were held in order to place the results at the disposal of the interested industrial field already in the preparation stage. Furthermore, the results were published in expert organs and presented on exhibitions.
Publications:
Schulz, H.; Würz, T.; Huerkamp, W.: Fatique of Tools in High Speed Milling. WGP-Annalen Volume VII/2. WGP-Selbstverlag 2000
Schulz, H.; Würz, T.; Huerkamp, W.: Safety Aspects of Fast Rotating Tools. In: Technologies of the XXI Century Machines Manufacturing. Springer, Berlin 2001
Further informations:
mechanical engineering
Type of hazard:mechanical hazards
Catchwords:Klein- und Mittelbetriebe, Mechanische Gefährdung, Sicherheitstechnik
Description, key words:high-speed processing, tools, cyclic load, material fatigue, use of aluminium alloys as basic body materials, further development of tool safety standardization