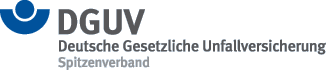
completed 02/2011
Replacement of EN 954-1, governing safety-related parts of control systems, by EN ISO 13849-1 resulted in a need for designers and manufacturers to be supported in implementing the requirements of the new standard. Owing to the consideration given to the probability of failure of the safety-related parts of a control system, creation of a machine control system to EN ISO 13849-1 is more complex than was previously the case. In order to offer support to its member companies, the German Machine Tool Builders' Association (VDW) had asked the Institute for Occupational Safety and Health of the German Social Accident Insurance (IFA) to evaluate model solutions for machine tools. In conjunction with the manufacturing companies, realistic examples were examined and typical safety functions of machine tools analysed. The results were used to provide the manufacturers with a library of safety functions by means of which company-specific solutions can be implemented easily. By making minor changes, for example by substituting different parameters for components, machine manufacturers are able to adapt the examples to their own machine controls. The manufacturers are thus assisted in satisfying the applicable standards and the requirements of the Machinery Directive.
The work conducted during the project was performed in working groups made up of representatives from the companies concerned, the VDW, the responsible expert committee and the IFA. The project was divided into work packages. A work package for each safety function comprised the following steps. Firstly, the safety function and the required Performance Level were defined. This task was performed by the former expert committees responsible for machine construction, production systems and steelwork (FA MFS), metal and surface treatment (FA MO) and machine construction, hoists, and foundries and rolling mills (MHHW). A schematic circuit diagram was produced, as was a description of the corresponding function of the example under consideration. The safety functions processed were set out by the relevant working groups. In the next step, a safety-related block diagram was produced, and the Performance Level determined and evaluated with the aid of SISTEMA. Finally, the design and functional parameters of the safety function were documented.
39 safety functions for machine tools were modelled, analysed and documented. As a result, typical safety functions for different types of machine tool are now available with documentation and a SISTEMA file. Machine manufacturers can take this documentation as a basis and use it to adapt their own machines.
mechanical engineering
Type of hazard:mechanical hazards
Catchwords:machine safety
Description, key words:functional safety, machine tools, practical aids to design, implementation of ISO 13849, VDW project, machine safety, Performance Level (PL), safety-related block diagram, PLC, controls, SRP/CS, probabilistic safety assessments