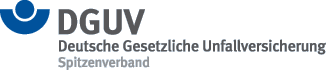
completed 02/2012
Nanomaterials are created in particular by thermal processes, where they take the form of emissions, (such as ultrafine particles (UFPs), given off during welding processes, or diesel soot or industrial waste gases), or are manufactured intentionally (synthetic nanomaterials) and added to industrial materials in order to endow the latter with particular material properties (for example for the manufacture of electrically conductive plastics, scratch-proof paints, etc.). Ultrafine particles/nanomaterials involve particles with diameters in the range from 1 to 100 nanometres. Should such particles enter the atmosphere, it may be assumed that owing to the lack of sedimentation processes, they remain dispersed as airborne substances for long periods of time in the ambient air. They may enter the human body, for example by inhalation. Evidence suggests that nanomaterials are the cause of numerous diseases. Their effects upon human health and the risks they present to the environment are therefore the subject of numerous research projects. In the interests of occupational safety and health, suitable measures must therefore be taken to reduce workers' exposure to nanomaterials to a minimum. Airborne substances which are released by work processes are usually separated by means of filtration equipment. This research project examined whether different types of conventional filter media used for the separation of dusts in filtration plants are also suitable for the separation of ultrafine particles.
On behalf of the Institute for Occupational Safety and Health of the German Social Accident Insurance (IFA), the nanomaterial filtration performance of a number of filter materials was examined by the Chair of Mechanical Process Engineering at the University of Kaiserslautern. A UFP generator was used to create ultrafine titanium particles which were dispersed within the airflow of a duct and applied to individual filter media. The filter media constituted a range of filter materials, the separation efficiencies of which had been tested beforehand with fine quartz dust (Dust Class M filters) and paraffin oil mist (Dust Class H glassfibre filters) in accordance with EN 60335-2-69, "Household and similar electrical appliances - Safety - Particular requirements for wet and dry vacuum cleaners, including power brush, for commercial use". UFPs were separated on round plane filters 90 mm in diameter. The airspeed in the dust canal was selected such that the flow conditions during testing were comparable or identical to filter loads commonly encountered in filtering separators. The particle number concentrations in the atmosphere were measured by means of a scanning mobility particle sizer upstream and downstream of each filter. The separation efficiencies were determined for the individual filter materials, based upon the concentrations.
Eight different filter materials satisfying the requirements of either Dust Class M or H to Annex A of EN 60335-2-69 were studied. The Class M filters consisted of the following materials: bonded fabric manufactured from polyester filaments, double-layer pulp containing synthetic fibres, corrugated cellulose, polyester needle felt with antistatic backing fabric, spunbonded/meltblown/spunbonded composite, and polyester spunbond and polytetrafluoroethene (PTFE) membranes. The Class H filters consisted of glassfibre or micro-glassfibre filter paper. Almost constant separation efficiencies approaching 1 (separation efficiencies of approximately 100%) were observed over the particle size range examined of approximately 20 to 300 nm. Conversely, the Class M filters exhibited an inhomogeneous separation capacity. In the UFP size range from approximately 20 to 300 nm, four M filters exhibited non-constant separation characteristics. For the pulp material containing synthetic fibres and for the cellulose filter, separation efficiencies of 0.6 were measured in the range from 20 to 40 nm. The separation efficiencies deteriorated progressively with increasing particle size, reaching only approximately 0.2 in the size range from 100 to 300 nm. Polyester needle felt and bonded fabric manufactured from polyester filaments exhibited superior separation characteristics. Around 90% of UFPs in the size range from 20 to 40 nm were separated (separation efficiency of 0.9); the separation efficiencies fell to as low as 0.3 with increasing particle size (size range 200-300 nm). The two other Class M filters exhibited separation characteristics approximating those of the Class H filters. A separation efficiency of approximately 0.97 was determined over the entire UFP size range for the spunbonded material. For polyester spunbond with PFTE membranes, the separation efficiency in the UFP range of 20-40 nm was also approximately 0.97; for larger UFPs (70-90 nm), it fell slightly to values of around 0.9. The results are consistent with those from filter material tests to EN 60335. The separation efficiencies of the Class H filters were higher than those of the Class M filters, as anticipated.
-cross sectoral-
Type of hazard:work-related health hazards
Catchwords:technical protective measures (exposure reduction/ protective devices)
Description, key words:nanomaterials, separation, filtermedium, ultrafine particles