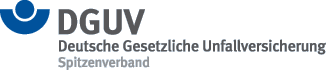
completed 03/2022
Exoskeletons have been used successfully for many years in medical rehabilitation, for example to allow those who have suffered spinal injuries to walk again. Recently, more and more exoskeletons designed especially for use in industrial applications are appearing on the market. These exoskeleton systems are intended to provide workers with mechanical support during strenuous activities, such as lifting loads or overhead work.
Although numerous laboratory studies have already demonstrated certain benefits of exoskeletons, the actual benefit they provide in industrial applications is still largely unknown. Firstly, it is not clear to what extent the postures tested in the laboratory really occur in practice in terms of their characteristics and duration. And, secondly, it is unknown whether and to what extent other necessary activities may be impaired by the exoskeleton.
Diverse experience from the fields of machine safety (such as collaborative robots) and personal protective equipment can be used to support the safety-related assessment of the use of exoskeletons. However, the exoskeletons available on the market often fail to give adequate consideration to the observations concerning safety, despite claims to the contrary by some manufacturers.
The Institute for Occupational Safety and Health of the German Social Accident Insurance (IFA) took part in the "Exo@Work" research project as part of a research cooperation between the Institute of Mechatronics of the University of Innsbruck (Austria) and the Expert Committee for Trade and Logistics of the German Social Accident Insurance. The aim of the project was to develop guidelines for the evaluation of exoskeletons for the world of work. A basic process for the evaluation of relevant systems was developed on the basis of a broad analysis of exoskeletons. The methodology for evaluation was validated through laboratory studies and field studies with representative exoskeletons. The exoskeletons were selected in such a way that it was possible to differentiate between the different approaches (e.g. different approaches regarding morphology [rigid exoskeletons/soft textile-based exoskeletons] and actuation technology [active and passive]) and this could be taken into account in the guidelines. This project established a basis for systematically evaluating exoskeleton systems in future with regard to their biomechanical, physiological and safety-related effects. This project focused on the use of exoskeletons that support the trunk and hip. In another project (IFA 4236: Exoskeletons), exoskeletons for the upper extremities were examined using a comparable method.
In this project, the work carried out by the Institute for Occupational Safety and Health of the German Social Accident Insurance involved performing a biomechanical analysis of the useful effect of exoskeletons that support the trunk and hip, ergonomic evaluation of the exoskeletons in industrial applications and determining the aspects that must be considered during the risk assessment. In accordance with European statutory regulations, the risk assessment must be carried out by the manufacturer as well as the employer utilising the exoskeleton. While carrying out this work, the Institute for Occupational Safety and Health of the German Social Accident Insurance also contributed its expertise as a Notified Body under the Machinery Directive (EU 2006/42/EC) and under the PPE Regulation (EU 2016/425).
Using a combination of laboratory and field measurements, the Institute for Occupational Safety and Health of the German Social Accident Insurance determined the effects of various exoskeletons on musculoskeletal workloads in the back using an inverse dynamics model and electromyography (surface EMG). To this end, as part of an intervention study, twelve test subjects (six men and six women) performed various static and dynamic lifting activities with various loads (14 test variants in total) in a random order. During the study, two passive exoskeletons and one active exoskeleton were tested. In order to evaluate the effect the exoskeletons had on musculoskeletal workloads in the back, the following biomechanical parameters are used: muscular activity (EMG) of the lumbar and thoracic back muscles, the joint moment at the lumbar spine (L5/S1), compressive force applied to the intervertebral discs of the lumbar spine (L5/S1), ground reaction forces and the hip and shoulder joint angle. In an additional round of tasks, the feasibility of everyday movements was tested, such as walking, sitting down/standing up, lifting a small object from the floor, standing up from a lying position (simulation of movement after a fall) and independently putting the exoskeleton on and taking it off.
On the basis of the laboratory findings, the specific activity profiles in the cargo and baggage handling areas of several logistics companies were recorded over multiple hours using a movement measurement system (incl. EMG) that is worn on the body, and then analysed in order to be able to quantify the biomechanical useful effect of the exoskeleton used. As part of this process, the measurement setup had to be specifically adapted for each exoskeleton in order to be able to measure the body posture and body movements as well as the movement of the exoskeleton. Parallel to this, the subjective reduction in musculoskeletal loads and potential problems in relation to discomfort caused by wearing the exoskeleton were recorded by means of user surveys.
As part of the project, the Institute for Occupational Safety and Health of the German Social Accident Insurance developed a risk assessment for exoskeletons and their use and tested it using representative examples. This risk assessment was first made available to cooperation partners and is now available as a model template to download on the homepage of the Institute for Occupational Safety and Health of the German Social Accident Insurance. This model risk assessment is intended to make the risk assessment process easier for the responsible people and thus is an important contribution to the safe use of exoskeletons in practice.
The laboratory studies demonstrated significant reductions in the load placed on the back of between 10 and 30% in relation to the load peaks for all exoskeletons tested. This was also demonstrated for the biomechanically measured joint moments and the compressive force applied to the intervertebral discs of the lumbar spine as well as EMG activity in the back extensors. The direction-dependent torque curve of the relevant exoskeleton plays a crucial role here. The characteristic curves show that the exoskeletons only ever partially support the trunk and only provided significant load relief at larger trunk bending angles (approx. 30° and above). For passive exoskeletons especially, it is notable that, due to the inevitable hysteresis effect, the amount of support provided while straightening up is significantly lower than the support provided while previously bending. When it comes to active exoskeletons, this hysteresis effect can generally be compensated for through the drive unit. However, due to the drive control system, the full drive power is only provided after a delay, which is particularly noticeable at the start of a lifting process, since this is the point at which the highest loads on the back are recorded.
Due to the coronavirus pandemic, it was not possible to perform as many operational measurements as initially planned. The load relief effect of the exoskeletons was less pronounced in industrial applications than in the laboratory tests. This is due to the fact that, in addition to the main, load-heavy activity, the industrial applications also involved secondary activities, such as working in an upright position, walking etc. In particular, no supporting effect is provided when carrying loads. In contrast, as with walking, the exoskeletons have more of a disruptive effect in this case.
The developed methodology should be used in further operational measurements, in order to determine best-practice examples for the use of trunk-supporting exoskeletons. At this point, the developed guidelines can help practitioners in the industrial sector to more easily evaluate the use of exoskeletons in workplaces that are under consideration. Furthermore, in future, appropriate practical scenarios with regard to the time spent wearing an exoskeleton must be developed, in order to achieve both a relevant reduction in musculoskeletal workloads as well as a high level of user acceptance.
-cross sectoral-
Type of hazard:work-related diseases
Catchwords:stain, load, working equipment
Description, key words:Exoskeleton, stress, musculoskeletal system