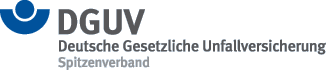
completed 12/2019
Numerous limit values (including the general dust limit value and the occupational exposure limit for manganese) have been lowered in Germany in the recent past, and risk-based limit values introduced for metals and metal compounds classified as carcinogens. These new limit values particularly apply to plants in which metal workpieces are processed by welding, cutting and allied processes. Measurements conducted by the German Social Accident Insurance Institutions have shown that the limit values cannot always be observed at welding workplaces, even when protective measures are taken. The available measurement data do not reveal the welding parameters and working conditions sufficiently. Knowledge about the effectiveness of measures to reduce welding fume exposure or to observe limit values relevant for welding processes does not exist.
The aim of the pilot study is to determine whether, and subject to what preconditions, the limit values for metals can be met during welding work.
The results are to be incorporated into the Interweld study, which is to be conducted at a later stage by the IPA. The Interweld study is to comprise three steps. Firstly, the existing situation in around 20 metalworking companies in Germany is to be determined. Secondly, the companies are to be advised on the implementation of protective measures, taking into account the results of the pilot study. Finally, the effectiveness of the measures in the companies is to be reviewed once after the recommended protective measures have been implemented.
During the pilot study, welding operations were simulated under realistic conditions and with application of the technical protective measures currently available. During the simulation, components specially designed for the pilot study were performed by a MAG-welding process carried out by a welding trainer in the IFA's mechanical workshop. The components were fabricated from mild steel (material No 1.0038) and high-alloy chrome-nickel steel sheet (1.4301). The mild steel sheets had thicknesses of 2 and 10 mm, the chrome-nickel steel sheets 3 and 10 mm. Each component required the welding of fillet welds, upward and downward vertical welds, an overhead weld and a build-up weld. The welding parameters were defined in advance for each weld. Components fabricated from 2 and 3 mm sheet were welded by short-circuiting arc or modified short-circuiting arc, those fabricated from 10 mm sheet by spray arc transfer, modified spray arc transfer, pulsed arc and modified pulsed arc. The welding parameters of welding current and voltage, wire feed rate, shielding gas volume flow rate, arc burn time and electrical energy were recorded in all welding tests by means of a data logger. For each welding test, the total length of all weld seams was approximately 8 m and the welding time approximately 1 hour. Individual tests employing PIMEX (Picture Mix Exposure; video recording and measured data logging) were carried out to document the welder's working method and his exposure to welding fumes.
The welding fume emitted by the welding processes were extracted by means of different extraction devices (two welding torches with fume extraction produced by different manufacturers ; a tracking extraction hood mounted on a support arm). All fume extraction devices were operated as intended: for example, the extraction volume flow rates on the welding torches were set according to the manufacturer's specifications or the ISO 21904-3 standard. The workshop was ventilated by a central technical ventilation system. An air exchange rate of approximately 2 h-1 was measured in the workshop.
In each test setting, the exposure of the welder was determined by air sampling at the person. The concentrations of welding fumes and manganese were measured in the respirable dust fraction; during welding of the chrome-nickel steel sheet, nickel and chromium and their respective compounds and chromium(VI) compounds were also measured (in the inhalable dust fraction). Parallel to performance of the exposure measurements, the welding fume concentrations in the workshop were determined at three measuring points in order to permit conclusions regarding the spread of the fumes in the workshop and thereby the exposure of other persons present in it.
In addition, the emission rates (quantity of welding fume emitted per unit time) of the individual welding processes were determined in separate measurements.
The welding tests performed showed that exposure to welding fumes during MAG welding can be reduced efficiently by the use of extraction equipment and optimization of the welding process. Observance of the limit values was however not possible at all settings.
During MAG welding of 2 mm mild steel sheet, the welder's exposure to welding fumes was below the general dust limit. Violations of limit values, including for manganese, were noted during tests in which welding wire with a high manganese content (approx. 7%) was used.
During welding of 10 mm mild steel sheet, the welder was exposed in almost all tests to values above the limits for general dust and manganese. The limits were observed only with use and careful positioning of the tracking extraction hood.
The welding fume concentrations in the workshop lay below the general dust limit; only the occupational exposure limit for manganese was exceeded in the workshop atmosphere at certain settings, for instance when 10 mm sheets of mild steel were welded.
During welding of 10 mm chrome-nickel steel sheet (pulsed arc, modified pulsed arc), the welder's exposure to welding fumes lay below the general dust limit value at all settings. The limit value for manganese however was exceeded at all settings. The assessment criterion for chromium(VI) was seen to be violated during pulsed arc welding. Modified pulsed arc welding proved to be associated with lower emissions; the limit value was observed in this case.
During welding (short-circuiting arc, pulsed arc) of chrome-nickel steel components (3 mm), the manganese limit value was observed when fume extraction equipment was used. Violations of the assessment criterion for chromium(VI) compounds were however noted in 7 out of 9 test settings and violation of the nickel limit value in 5 out of 9 settings.
Only sporadic violation of the limit values was determined in the workshop atmosphere during welding of chrome-nickel steels.
Conclusion: The energy of a welding process significantly influences the emissions of welding fume and thus the exposure of welders. An emission rate of 12.6 mg/s was measured for MAG welding of 10 mm mild steel by spray arc welding and a welding current of 350 A. Where welding is carried out at a lower welding current, the emission rate is reduced considerably (170 A = 1.4 mg/s). A welding fume emission rate of approximately 0.2 mg/s was determined for short-circuiting arc welding of 2 mm sheet (approximately 90 A).
MAG welding processes require optimization of the welding process parameters and the use of extraction equipment in order to observe the limit values for metal. Both the extraction equipment and the parameters of the welding processes must be improved.
metal working
Type of hazard:dangerous substances
Catchwords:limit value
Description, key words:welding fumes, welding, manganese, nickel, metal, limit values, exposure, local exhaust ventilation, LEV, ventilation