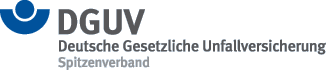
completed 08/2003
The design of guards on grinding machines is of decisive importance for the protection of operators and surrounding machinery against ejected fragments of bursting grinding wheels. EN 13218, "Machine tools - Safety - Stationary grinding machines", stipulates the minimum wall thickness of guards on stationary grinding machines. These values are based to a large extent upon experience and estimates, and not upon experimental testing. The standard contains an attestation procedure representing an alternative to the use of wall thickness tables. The attestation procedure requires that actual grinding wheels be burst at the maximum operating speed within the guard in order to permit evaluation of the latter's impact resistance. This time-consuming and expensive process leads, however, to results with poor reproducibility. The objective of the project launched by the Metal and Surface Treatment expert committee was to develop an impact test procedure which is as simple as possible for evaluation of the impact resistance of guards on stationary grinding machines.
An impact test procedure for guards on stationary grinding machines was developed in three stages, to be carried out to some degree simultaneously. An existing pneumatic impact test device was first used to determine the impact resistance of steel plate (St 12.03, a typical material for guards) and polycarbonate (a common vision panel material) by means of impact tests employing cylindrical projectiles manufactured from grinding wheel ceramics. The projectiles were varied in their strength, mass, dimensions, geometry and other characteristics. The second step involved the development of steel projectiles yielding impact results comparable to those of ceramic projectiles. The benefits of steel projectiles lie in their simpler manufacture and in their facility for re-use following an impact test. The third stage involved validation of the impact results by overspeed tests employing actual grinding wheels loaded up to their burst speed.
The protection offered by guards against projected fragments of grinding wheels is dependent upon a number of mutually influencing parameters. The impact resistance of the guards is determined in such cases not only by their dimensions and the strength properties of the materials employed, but also and to a greater degree by the properties of the fragments impacting upon them. The impact tests performed showed clearly that the impact strength drops with rising strength and sharpness of the ceramically bonded fragments. The influence of these factors was stronger in impact tests performed upon sheet steel than upon polycarbonate. In consideration of the tests performed, it is proposed that shot tests involving cylindrical steel projectiles similar to those performed on lathes (DIN EN 12415 "Safety of machine tools - Small numerically controlled turning machines and turning centres") also be employed to test the impact resistance of machine guards on stationary grinding machines. The diameter and masses of the projectiles and the shot velocities to be employed are selected on the basis of the width of the grinding wheels under consideration, and the maximum anticipated translational energy of the fragments in the event of a failure. According to current knowledge, such steel projectiles permit a conservative estimate of the impact resistance of guards on stationary grinding machines.
Further informations:
mechanical engineering
Type of hazard:mechanical hazards
Catchwords:Maschinensicherheit, Mechanische Gefährdung, Prüfverfahren
Description, key words:stationary grinding machines, guards, impact resistance, impact tests