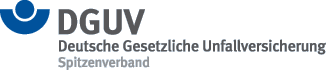
completed 01/2014
A force/pressure gauge is required for laboratory and in-plant measurements by means of which the limit values formulated in the BG/BGIA recommendations on the design of workplaces with collaborative robots can be checked. A complete instrument was to be developed based upon conventional principles for the measurement of closing forces and also permitting measurement of the pressure distribution generated by the impulse of the force. The instrument must be capable of modelling the biofidelic properties – i.e. the mechanical properties of the human body – of the individual body regions in accordance with the BG/BGIA recommendations. The biofidelic properties to be simulated here are essentially the deformation properties of the average human body. The deformability of the body structure behind the point of stress on the body must be considered, besides the local compression property of the point of stress itself. A suitable arrangement for recording and interpreting the measured data was to perform evaluation against the limit values immediately following measurement. For this purpose, a software application was to be developed by means of which the measurements and all necessary calculations and evaluations could be performed in accordance with the specified criteria. All test conditions, the measurement signals, further interpretations, and the evaluations were to be documented in a test report.
As is usual with closing force measurements, the basic concept of the force-pressure gauge took the form of single-axis measurement of the total force for the measurement of pinch forces or fast impulses. Measurement of the pressure distribution on the contact surface during the collision impulse was also implemented. The contact surface of the gauge took different forms and permits pressure measurements on a surface area of up to 300 × 300 mm. Plastic plates were adapted to this rigid contact surface for simulation of the local deformability of the local discrete body regions. The rigidity of the outward-facing plastic body was combined with an inward-facing linear spring according to the body region concerned, thereby enabling the overall rigidity of the body region to be modelled. The pressure distribution was measured by means of pressure measurement film resting on the outer surface of each plastic block. Two film measurement systems were integrated into the gauge. In the case of FUJI pressure measurement film, the collision pressure is reflected by variation in the red colour density within the film. The red colour density is digitized by means of a scanner and converted to a pressure distribution. The second pressure measurement system employed Tekscan pressure measurement film. In this system, pressure distributions are measured at a sampling rate of up to 700 Hz and with a geometric resolution down to below 1 mm². The parameters for evaluation in accordance with the BG/BGIA recommendations were determined from the interpreted pressure distribution and the measured impact/pinch force.
In the KDMG-KOLROBOT IFA force-pressure gauge, a biofidelic gauge has been developed that can be used for validation of collaborative work tasks during risk assessments of workplaces involving collaborative robots. The gauge can be used to simulate critical collision processes and to measure the strain criteria of "maximum total force" and "maximum pressure at the collision surface", and to evaluate these values in accordance with the BG/BGIA recommendations for the design of workplaces involving collaborative robots. The hardware and software provide comprehensive facilities for measurement and analysis for the purpose of risk assessment. The gauge provides a practical means of simulating the biofidelity of individual regions of the underlying body model. The results of collision measurements together with all underlying conditions are documented in a detailed test report, which is saved in the form of a PDF file. By virtue of its technical design, which satisfies the specifications derived from the recommendations, the gauge constitutes a sound basis for a standard method for the measurement of collision processes that is reproducible and consistent with the standards. The relevant properties of the gauge are to be introduced into standardization work. The gauge can thus be used to test compliance of the safety requirements with the provisions of standards in accordance with the current state of the art. This has been confirmed by the use to date in the ongoing testing and certification of workplace applications involving collaborative robots. The modular design of the gauge is conducive to further development. Further gauge types can be integrated. The same applies to the measurement properties and components. The design principle will enable new scientific findings on limit values or extended biofidelic properties of the human body to be incorporated in the future. When suitable workplace design measures are taken or the robot system is suitably parameterized, the gauge enables the stress upon the body during a collision process to be reduced below the stress limit values stated in the recommendations.
-cross sectoral-
Type of hazard:mechanical hazards
Catchwords:accident prevention, risk assessment, measuring methods
Description, key words:measurement method, collision risk, severity of injury, limit values, force measurement, pressure measurement, biomechanical strain