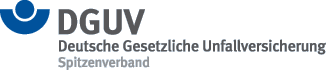
completed 07/2011
A pain threshold map is required for evaluation of permissible mechanical stress limits at the human-machine interface. Workplaces employing collaborative robots presenting certain residual collision risks are an important area of application. In order to determine a human pain threshold map based upon mechanical exposure of various regions of the body, an algometry test facility is to be developed. The test facility is to permit flexible and extremely variable positioning of a test subject with complete immobilization of individual body points. The mechanical stress is applied to the body point by means of a fully automatic algometer. Suitable software is to be developed for parameterization of the algometer, for the measurement procedures, and for structured recording and archiving of all relevant data. Determining of the pain threshold involves measurement of the total force and the pressure distribution at the contact surface between the plunger and the surface of the body.
For measurement of test subjects' pain thresholds, a large-volume facility was developed permitting all necessary body postures with immobilization of the body points to be stressed. A linear motor with a special plunger was employed for precise application of the force stresses. The test facility enables stress tests to be performed with pain thresholds of up to 500 N. The control system applies a stress in the form of a linear force ramp within the range from 5 to 20 N/s. By means of a thrust axis, the linear motor permits a penetration distance of approximately 120 mm at the body point. The measurement accuracy of the force is +- 1 N, that of the distance +- 0.01 mm. The test facility was developed such that the body points can be adjusted/positioned flexibly, and the stress applied with a defined ramp characteristic up to the pain threshold. In the individual tests, the force and the pressure distribution on the plunger are measured up to the pain threshold. The software was developed for control, recording of the measured data, monitoring of the safety, archiving and documentation.
A test facility was built for measuring human pain thresholds and for laboratory use. The test facility contains a large-volume chamber to accommodate the test subject and in which any desired body point can be positioned and immobilized. For immobilization, two vacuum mattresses with pump units were procured which can be fixed and operated on the rear contact surface of the chamber. For application of the stress, a fully automated algometer was developed for generation of force ramps up to 500 N with linear correction on the body point. When the pain threshold is reached, the test subject switches off the stress rise, and the algometer is rapidly reversed to a safe initial position. During stress application, the force/distance/time signal is recorded for subsequent interpretation. A safety facility was also developed which safely monitors the entire operation of the algometer. The facility is based upon a limit force, selected by the user, which cannot be exceeded on the test subject. A control panel with PC workstation was developed and built housing all items of control, measurement and safety equipment. For performance of the discrete pain threshold measurements, a test control program was developed by means of which the comprehensive adjustment, control and measurement steps are completed under systematic control, and the measured data automatically saved and archived. The test facility ensures that pain thresholds are measured systematically with very high reproducibility of the measurement procedure. By use of the test facility as the basis for a future DGUV project, a comprehensive pain threshold map can be created. The pain threshold map can be used to validate the stress limit values found in the recommendations of the IFA and the accident insurance institutions for the design of workplaces involving collaborative robots, and for more advanced assessments involving biomechanical issues relating to the human-machine interface. A declaration of conformity is being drawn up for the test facility's compliance with the safety requirements of the Machinery Directive, and the CE mark issued.
-cross sectoral-
Type of hazard:mechanical hazards
Catchwords:industrial accident, measuring methods, design of plants and procedures
Description, key words:machine guarding, collaborative robots, instrument