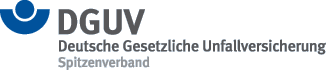
completed 06/2021
Human-robot collaboration (HRC) is a key theme for Industry 4.0. Personal safety is an important criterion when it comes to human-robot collaboration. Protective measures for HRC robots will only be accepted by users if they also enable efficient processes along with the expected level of functionality. The research project RoKoRa (Safe Human-Robot Collaboration using High-Resolution Radars) – which was funded by the German Federal Ministry of Education and Research (BMBF) – aimed to present a concept for human safety by demonstrating a high-performance solution involving the collaborative use of an assistance robot. The safety requirements for the specific application are a key topic in any HRC robot system. In this project, the specific application had to be chosen and the relevant safety issues had to be considered. The aim of the project was to demonstrate a safety concept for use in robotics applications involving high load capacities and fast movement speeds for which no safety products are currently in use or available on the market.
RoKoRa joint project: Development of a sensor system in which egocentric sensors mounted on the robot arm enables optimal, situation-dependent adaptation of the movement speed (listed as a protective measure in DIN ISO/TS 15066: Collaborative robots) and movement direction of the robot by detecting proximity between body parts/objects in the environment and parts of the robot through distance and speed monitoring. The aim of such a sensor system is to enable user-friendly, efficient collaboration.
Selection of an example application from the field of automotive manufacturing (in this case: mounting of brake discs) including analysis of the relevant safety requirements. Construction of a demonstrator.
DGUV/IFA sub-project: Conducting assessments of the “Functional Safety” of the application specifications, the safety concept and the sub-components of the sensor system during development and in a way that is oriented around the project milestones; generic standards should be used as a reference (DIN EN / IEC 61508, DIN EN ISO 13849, DIN EN 61784-3, DIN EN 61496, etc.).
The joint project resulted in the development of a prototype sensor system with a sensor ring consisting of 16 radar sensors for a robot arm with a sensor data network, including interfaces and relevant communications protocols/data structures. The project involved creating a functional representation of the sensor system on the demonstrator using the components developed as part of the sub-projects, and, in addition to the development of mechanical elements such as the sensor ring, the grippers, the workpiece and the robot, it also involved the development of a distance-based movement control system for the robot as well as commissioning and function testing of the robot. The performance figures achieved with the demonstrator resulted in a detection capability of 40 mm to 55 mm at a distance of up to 1.2 m and a range resolution of 40 mm. The latency of the sensor system is 100 ms. These performance figures meet the relevant requirements for the example application. The safety integrity level (SIL 2, PL d, HFT 1) largely complied with the generic safety standards and the requirements of the DIN EN 10218-1 standard for industrial robots.
The project represents an important contribution towards enabling progress in the field of human safety during human-robot collaboration, which is a key topic of the “Autonomous Robots for Assistance Functions” funding campaign of the Federal Ministry of Education and Research (BMBF). In this case involving an industrial context with high payload robots, it was possible to demonstrate that a protective measure for a robot can be implemented in accordance with user requirements and expectations during the development phase.
This offers an imminent commercial value for the development partners involved in the project – here: Further development of DIN ISO/TS 15066 - Suitable protective measures for cobots.
vehicle construction
Type of hazard:design of work and technology
Catchwords:new technologies, Sicherheitstechnik, Technische Schutzmaßnahmen (Expositionsminderung/Sicherheitseinrichtungen)