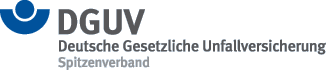
completed 10/2004
The ergonomic aspects of machines already form the subject of many standards and other projects. The basic standards available were first classified, revealing gaps and deficits. A structure extending from basic standards to product standards was introduced. Second, a guide to assist product standards developers in the application of ergonomic standards during the design of machinery was drawn up in the form of prEN 13861:2000 "Safety of machinery - Guidance for the application of ergonomics standards in the design of machinery and for the drafting of ergonomics clauses in standards". The subject of ergonomics has therefore been addressed and intensively adapted from the perspective of standardization. These activities have not yet provided test and certification institutes with a satisfactory solution for the treatment of ergonomics on machinery in real-life testing. The existing requirements and definitions are often too general and exhibit gaps or even contradictions. It is not easy for testers to summarize and apply requirements originating from many sources. Designers of machinery correspondingly lack clear guidance on how to attain conformity with the Machinery Directive. This project is intended to help close this gap. A checklist for ergonomic design of selected machines was drawn up at the BG Institute for occupational Safety and Health (BIA). It is based upon the most important standards, generally accepted scientific findings, and the BIA's own research. An interdisciplinary team of experts from the areas of occupational biomechanics, man-machine interfaces, and machine safety was formed for the purpose of this project. The objective was to develop a checklist which is binding upon the test and certification bodies and which these bodies are able to apply in practice. Since the rules and findings in this area are subject to continual change, the facility for subsequent updating had to be implemented from the outset.
Numerous standards and scientific findings exist. All relevant requirements were therefore first identified. These in turn were used to draw up a complete list of the identifiable check points. Only a selected number of check points could be formulated in detail for use in the checklist if application was to remain feasible in practice. The task of researching and formulating the check points was accompanied by large-scale inspections of machines, in order to assure the relevance and suitability of the checklist for practical application. Particular attention was attached to sound planning and evaluation of the checklist. This assured that the checklist itself is designed ergonomically. It must also be suitable for application by the uninitiated in the area of ergonomics. A comprehensive guidance document was therefore also produced. A database application was created as a tool for collection and processing of the information; this will enable work to be performed in parallel whilst assuring consistency. This tool will enormously simplify future updating of the checklist.
The results of the project take the form of a checklist with an assessment form, and a booklet of comments. The checklist will first be applied in a BG-Prüfzert test body prior to further publication.
Further informations:
mechanical engineering
Type of hazard:Arbeitsbedingte Gesundheitsgefahren, Mechanische Gefährdungen, Gestaltung von Arbeit und Technik
Catchwords:Ergonomie, Maschinensicherheit, Prüfverfahren
Description, key words:ergonomic design, checklist, machine safety, work-related health hazards, mechanical hazards, CNC machining centres and fully automatic lathes, conventional manually operated lathes, milling machines, box-column drilling machines, hacksawing machines, folding presses, guillotine shears