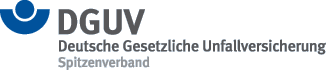
completed 12/2000
Highly automated production systems on machining centres, lathes, milling machines and robots require direct intervention by human beings, for example during set-up mode. The hazards resulting from impermissible machine movements must be prevented by the functions "safe standstill", "safe operational stop", "safely reduced speed", "safe cams", etc. On conventional machine control systems, the positions and movements of the machine axes are monitored by external switching devices (rotational speed monitors, standstill monitors, position switches). In more modern control concepts, these monitoring functions are assumed by the machine controller with a corresponding safety software and on the whole with the existing hardware. The task of the project, launched by the "Iron and Metal II" BG expert committee, was to demonstrate that control systems of this type deliver safety comparable to that of conventional designs.
As no regulations existed for the assessment of these new technologies, test principles and assessment criteria were drawn up on the basis of a number of projects. Machine controls from a number of German manufacturers were examined at numerous stages of development, from the concept phase through to series production. A single specification, for example, passed through up to ten individual audits. Following acceptance of the specification (assessment of concept) by the BG Institute for Occupational Safety (BIA), it was released for further development in which each step (conceptual design phase, detailed design phase, software design, hardware design, etc.) was monitored. In addition to extended tests on functional prototypes, discussions were also held with machine manufacturers, and the control system tested on selected pilot projects.
The use of microprocessors, already present in modern machine control systems, for redundant safety-related signal processing enables a level of safety to be achieved which is comparable to that delivered by conventional external monitoring equipment. In addition to the low cost of installation, integrated safety technology delivers enormous benefits owing to its reduced response time in comparison with that of conventional technology. The integration of safety-related functions into the standard controller also increases the acceptance among users.
Further informations:
metal working
Type of hazard:mechanical hazards
Catchwords:Maschinensicherheit, Sicherheitstechnik, Prävention
Description, key words:test principles, assessment criteria, concept generation phase, specification, audit, concept assessment, conceptual design phase, detailed design phase, software design, hardware design, safe power drive, safely reduced speed, safe operational stop, safe standstill, safe software cams, set-up mode