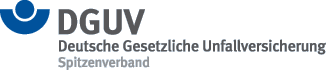
completed 07/2003
Owing to their composition (tin, lead, colophony, amines, formaldehyde, phenol, hydrogen chloride and carbon monoxide), the fumes arising during soldering may lead to irritation of the respiratory organs and the eyes and to other hazards to health. Studies were performed on a standardized test bench in order to identify the systems best suited to reduction of the soldering fume concentration at manual soldering workstations. The state of the art of soldering fume exhaust units was identified.
The emission rate arising during soldering was studied in accordance with DIN 33896-1, "Dust emission of technical equipment - Determination of the dust emission rate of machines intended for the use on work tables - Part 1: Basic method", both with and without soldering fume exhaust equipment. The results reveal the corresponding capture levels. The fume emissions were measured. The gas emissions were also to be measured, formaldehyde serving as the key component.
Soldering fume exhaust units can be classified into two basic types: the hood exhaust type and the point exhaust type. In the case of hood-type exhaust units, the capture facility is positioned in the vicinity of the soldering point with the aid of an articulated arm. In the case of point-type exhaust units, an exhaust tube is attached directly to the soldering iron, enabling the exhaust inlet to be positioned very close to the tip of the latter. Assessment of the soldering fume emissions revealed that the point-type exhaust unit initially worked very effectively, but that deposits in combination with the low exhaust cross-section caused its suction power to drop substantially over less than eight hours. Filters and fans were integrated into the hood itself of a number of the hood-type exhaust units studied. The fume filtration performance of these units was unsatisfactory. The best results were delivered by hood-type exhaust units employing a powerful fan in combination with two filter stages for particles and gas, as these units delivered a good filtration performance in conjunction with a low maintenance requirement. In view of the service life of particle filters and the risk of deposits leading to blockage, soldering fume filters should be equipped with a minimum volumetric flow monitor. The service life of the gas filter should be monitored by an operating hours counter which can be reset each time the gas filter is replaced. The study showed the gas emissions to be too low for measurement or analysis.
Further informations:
electrical engineering
Type of hazard:Gefahrstoffe, Arbeitsbedingte Erkrankungen, Arbeitsbedingte Gesundheitsgefahren
Catchwords:Maschinensicherheit, Prüfverfahren, Normung
Description, key words:safety of machinery, test method, standardisation, soldering fumes, health hazards, reduction of pollutant emissions, capture efficiency, separation performance, service life