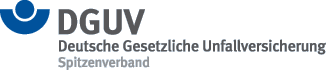
completed 03/2018
Any work accident causes in addition to personal pain and disability also economic losses due to work-related downtime and treatment costs for employers and society. This represents a high risk, especially for small and medium-sized companies. Therefore, it is important to identify potential dangerous situations at an early stage and to avoid them by means of preventive measures.
The aim of the project was, on the one hand, to identify principal methods of image analysis to increase occupational safety when using engine-powered industrial trucks. Different methods should be developed, evaluated and compared in terms of their effects, reliability and efficiency. On the other hand, a manufacturer-independent demonstrator assistance system was developed which demonstrated that occupational safety can be increased with 2D and 3D image processing. This assistance system can be retrofitted to any manually operated forklift truck from any manufacturers and can therefore be used in a variety of industries in the future. Here, a very high independence from proprietary, vehicle-own sensors is achieved, whose integration represents a challenge in retrofitting today. Furthermore, the image analysis methods are designed taking into account the diversity of the intralogistic working environments without being limited to a single environmental scenario.
First of all, an analysis of different methods to increase safety at work on motorized industrial trucks was carried out. Subsequently, based on an analysis of the existing accident data with industrial trucks, critical areas in the work area of the industrial truck as well as situations that frequently resulted in accidents were identified. Based on this analysis, the assistance system to be developed was identified and designed as a part of a system design. In addition to the technological components for the sensors and evaluation algorithms, various measures were also made for designing the interface to the driver of the industrial truck. For the simulation of the sensor data and the adjustment of relevant test cases, a realistic model of a dynamic storage environment was developed. Here forklifts and people can move arbitrarily and sensor data from these situations can be simulated. The data is automatically labeled and used to develop the methods. The development of the analysis methods focused on two different approaches, each of them combines a collision detection system with a module for person detection. On the one hand, classical methods for image processing were examined with regard to their suitability for the application. In addition, current developments in the field of artificial intelligence were taken up and approaches were developed based on different types of deep neural networks. All approaches were evaluated within laboratory conditions using demonstrator systems. The last step in the project was a field test within an industrial work environment.
In the first step, different types of interaction options with a truck driver could be systematically analyzed. As a result, a concept for a tactile warning system was developed. The sensor simulation software was able to virtually simulate any logistical scenarios and to generate training data. The analysis of the classical methods of image processing showed the basic suitability for the application, but often false detections that might reduce the acceptance of the driver of such a system. The approach using deep learning methods achieved very good results in the laboratory and field tests with regard to recognition quality with a very small number of misdetections. When trained with the simulated data, the approach is also independent of a specific application scenario and therefore transferable to different locations. The overall result is an assistance system that, by using modern sensor technologies, can reliably monitor a critical area, for instance behind the driver, to detect people and warn the driver accordingly. The use of a tactile interaction channel also means that the driver is not overloaded by an additional audio-visual interaction channel.
-cross sectoral-
Type of hazard:mechanical hazards
Catchwords:prevention, equipment safety, transport and traffic
Description, key words:PräVISION, floor conveyor, assistance system