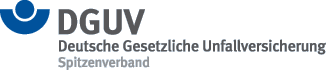
completed 09/2023
A production line with film or foil machines has commonly accessible areas where the film runs over unpowered guiding rollers, which are often potential hazard points. Such areas are known as pull-in points. The hazards of reaching into such a nip point have so far been described rather rarely, if at all. If a person reaches into a nip point, an extremity of their body – often upper extremities – can be pulled in, so that the person can no longer extricate that limb by themselves. This can lead to injuries ranging from minor to serious, and it is even possible for an extremity to be torn off. The issue is well known, but so far there has been no adequate basis for assessing such a risk.
The expected pull-in forces are to be determined or measured for typical configurations of pull-in points using a calculation and a test device so that the operator and the supervisor can make a targeted assessment of the hazard.
Both the operator and the manufacturer should carry out a risk assessment at an early stage, during the conceptual and design phases of a film wrapping machine, and it therefore seems appropriate to develop a mathematical model based on different operational and impact structures of the machine. This would make it possible to anticipate and prevent hazards early, even before a film or foil machine is commissioned.
A detailed review of the literature and a survey of manufacturers provided an overview of the properties that need to be taken into account for hazards at pull-in points. Also, a range of case-specific upper limits have been identified, based on the maximum forces a person would need in order to extricate a limb from such a hazard point.
On this basis, a model that takes into account considers relevant influencing variables, can be used to estimate the pull-in force at nip points. An examination of the pull-in forces for different friction constellations of a test body in combination with different film materials (e.g. polyethylene (PE), polypropylene (PP)) and film thicknesses between 50 µm and 200 µm were to be investigated. At the same time, the process speed (from 10 to around 100 metres per minute) should gradually be increased, either until a critical stress level is reached or until the film web breaks. Other parameters that can be varied are the wrapping angle, the web tension and the shaft diameter of the roller. To validate the model, a test device has been developed that can measure the load exerted on a test body during contact with a film winder. By varying the parameters, it should be possible to enhance the model in a series of incremental changes.
Using published studies on the forces of the human body during pulling movements on an upper extremity, certain pull-in forces have been derived that are likely to be critical for a person’s ability to extricate themselves. Depending on the body’s position, gender and execution of the movement, the forces that have been identified are around 150 N (up to a maximum of 300 N).
To measure the pull-in forces, a measuring device is now available that simulates a test body being pulled into a nip point. The relevant pull-in forces have been measured for three films made from different materials (e.g. PE, PP, TPU) and also with different structures (e.g. two-ply) and thicknesses. An initial series of measurements involved two test bodies with different frictional properties and geometries (flat and wedge-shaped). The test body was gradually moved towards the hazard point in increments ranging from 10 to 100 mm. The wrapping angle was approx. 135° and the diameter of the cylinder was 120 mm. The resulting forces were dependent on the penetration depth and the prevailing web tension force (100N to 250N) and, depending on the configuration of the nip point, were above the critical force. At the onset of contact, an increase in force was measured, which could correspond to several times the web tension with increasing penetration depth. As the duration of contact increased, the forces dropped to levels that were within the range of the web tension. This was due to the control mechanisms within the film wrapping machine. When the test body was being pulled out, thus putting an end to contact, a slight increase in force was observed again. A tear in the film was only observed in a small number of instances involving thin film.
Next, a simple mathematical model was created to estimate the pull-in force based on the physical principles of the system, comprising a cylinder and a film web. Further validation will require the use of more data than has been gathered up to date, as the frictional properties of contact bodies often cannot be established with sufficient precision. Also, the influence of the wrapping angle will need to be analysed more closely, based on further measurements, using the measuring device that has been developed. All data should then be entered into a data pool that will serve as the basis for the risk assessment.
chemical industry
Type of hazard:mechanical hazards
Catchwords:prevention
Description, key words:pull-in points, pull-in hazards, foiling machines, risk assessment, "test hand", conception of a test facility
Clermont, M.: Entwicklung einer Messeinrichtung zur Ermittlung von Einzugskräften an Auflaufstellen von Folienmaschinen (Poster). DGUV-Forum Forschung der Unfallversicherungsträger, Nümbrecht, 6./7. Oktober 2022
Clermont, M.: Entwicklung einer Messeinrichtung zur Ermittlung von Einzugskräften. Nr. 0437, Ausgabe 12/2022, 2 S. In: Aus der Arbeit des IFA. Hrsg.: Deutsche Gesetzliche Unfallversicherung (DGUV), Berlin – Loseblatt-Ausgabe
Clermont. M., Zimmermann, J.: Estimating hazards of feed zones in transportation process of flexible foils on roller in foil machines – Literature research and conception of a measurement. 5th PEROSH Research Conference & Anniversary event (20 years PEROSH), 6-8 September 2023, Stockholm, Sweden