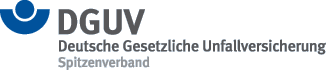
completed 01/2015
Sugar dust is produced at various stages during the manufacture and processing of sugar. At a sufficiently high atmospheric concentration, it can form a hazardous explosive atmosphere. The chemical composition of pure saccharose can be considered homogenous irrespective of the manufacturer and manufacturing process. The explosion safety parameters of sugar are determined essentially by the dust concentration and the particle geometry and size. In this project, the explosion safety parameters were to be determined systematically for a range of particle-size distributions and particle surfaces in order to determine a relationship between these parameters. The target variables were the lower explosive limit (LEL), the maximum explosion pressure (pex) and the rate of pressure rise (dp/dt). Based upon the relationships determined by experimentation, a simple model was to be developed for prediction of the explosion safety parameters for sugar.
The sugar dusts in the GESTIS-STAUB-Ex database were analysed, and a range for explosion parameters created. Defined particle-size fractions were produced from standard granulated saccharose by milling and sieving. Based upon EN 14034, the explosion parameters pex, dp/dt and LEL for these fractions were determined in the laboratory. Following the explosive reaction, gas samples from the combustion chamber were analysed for carbon dioxide, carbon monoxide and residual oxygen. Important information on the yield of the reaction was obtained from the concentrations of the gaseous reaction products. In addition, the calorific value was determined by calorimetry and the specific surface area of the different fractions by the BET method (determining of the surface area by gas adsorption). In a second test series, the change in the LEL was studied by systematic variation of the fine-dust components.
It was demonstrated that the maximum explosion pressure (pex) for granulated sucrose determined under standard conditions to EN 14034 correlates directly to the reactive surface area of the particles, with an uncertainty of ± 15%. The two variables of concentration and particle-size distribution are thus reduced to the magnitude of the surface concentration. The maximum explosion pressure pex for any desired sucrose particle size distribution can be read off on the diagram produced. It was not possible in the experiments to transfer the method to the rate of pressure rise dp/dt. The kinetic variable dp/dt is influenced by the mass of the particles and their dispersion in the reaction chamber, as well as by the surface area. The safety variables determined in the course of the project confirm and extend the data in the new edition of the guidance document issued by the German Social Accident Insurance Institution for the raw materials and chemical industry on the avoidance of dust explosions during the production and processing of sugar.
food industry
Type of hazard:dangerous substances
Catchwords:physical factors
Description, key words:sugar dust, particle-size distribution, BET surface area, rate of pressure rise (dp/dt), maximum explosion pressure (Pmax), lower explosive limit (LEL), dust explosion